(Date of birth not provided)
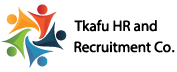
Certificates
Procurement & Supply Planning Tools & Techniques – Udemy Present
Basic & Intermediate Excel – EXCEL4US Training Center 06/2021
Certified Business Logistics Professional – American Management Institute 04/2021
IOSH Managing Safety – Jordan Engineers Association 07/2019
ISO 9001:2015 Quality Management System (Attendance) – Jordan Engineers Association 11/2016
Languages
Education
Professional Experience
Received a daily average of 25+ purchase requests, sourced purchases of materials to suppliers and
negotiated prices accordingly
– Received feedback from suppliers regarding availability of materials, discussed alternatives with the team
and issued 100s of purchase orders (POs) utilizing SAP
– Collaborated with the stock controller on needed materials, monitored and tracked data accordingly
– Analyzed and forecasted material requirements and maintained knowledge regarding the market prices to
plan purchases in advance
– Saved an average of 5% in costs of logistics and materials through analyzing current supplier contracts and
searching for alternatives
– Initiated relationships, conducted meetings and acquired 15+ new suppliers
– Reviewed company profiles of suppliers, gained product knowledge, and negotiated payment terms &
delivery methods
– Liaised with the Finance Department on processing supplier payments and followed up on documentation
– Issued Letters of Credit, contacted delivery vendors and followed-up on shipping and logistics matters
Liaised with the technical team to select the best materials to source that serve customer needs
– Contacted 10+ suppliers per order, compared proposals and selected best offers based on lead time,
quality and cost
– Negotiated with suppliers on cost and payment terms to increase ease of business, and issued PO for
suppliers for awarding tenders or RFQ
– Prevented delays and penalties by following through on submitting documents in a timely manner
– Collaborated with the management and Finance to identify the reasonable profit margins
– Followed-up with suppliers every 2 – 3 days on the manufacturing process and shipments
– Liaised with the Financial Department to follow-up on withheld payments by the customers
– Prepared 300+ commercial and technical offers for the requested orders
– Followed-up on shipping arrangements with suppliers and shipping companies or freight forwarders
– Reviewed, compared, analyzed, and approved products and services to be purchased
– Followed-up on banking procedures to secure payment with suppliers and end-users
– Contacted suppliers/manufacturers upon receiving orders, signed contracts, finalized prices, and
INCOTERM, and followed-up on manufacturing
Directed 25+ production line workers and planned shifts according to the needed output
– Supervised 10+ production lines for assembling TVs, Air Conditioners, Refrigerators & Washing
Machines
– Decreased the waste time by up to 15% and accelerated the production process through controlling shifts
– Controlled the input and output of production lines and the quantity produced as per the demands & plans
– Calculated the production quantity upon the available labor
– Coordinated with the Quality Control (QC) on the packaging process and supervision of production lines
– Liaised with the warehouses on controlling inventory based on demands and availability of inventory area